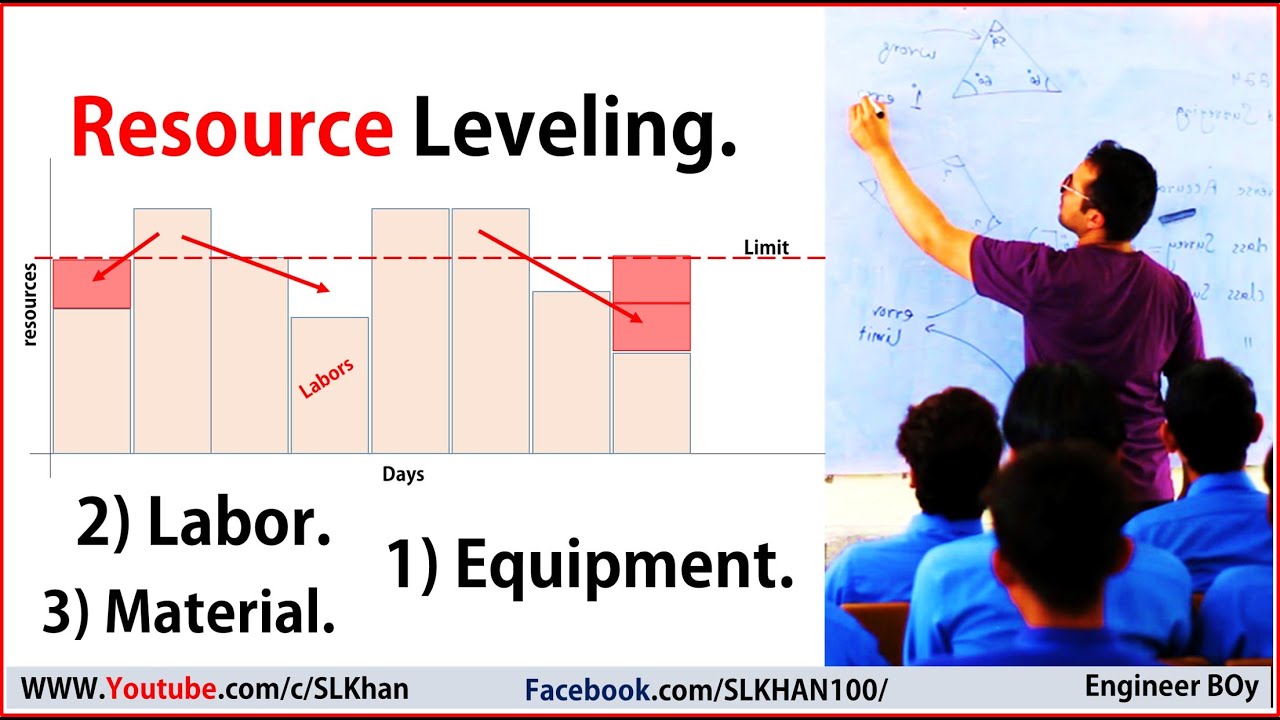
Accenture is the world's largest supply chain consultancy and has acquired GRA, a logistics and supply chains consulting firm. By combining these services, Accenture helps its clients meet the increasing demands of the modern supply chain. Accenture's supply chain specialists help clients create dynamic customer experiences while implementing responsible practices. Accenture has recently acquired Blue Horseshoe Group, and Xoomworks Group. We will be discussing the importance and role of supply-chain capabilities in modern business strategy.
Accenture's Supply Chain Strategy
Accenture recently completed the global supply chain strategy of MedShare International, a 501c(3) charitable organization that distributes surplus medical equipment in developing countries. The strategy was designed to optimize the entire supply chains, from procurement and sourcing to warehouse operations and customer interaction. The strategy will be implemented over many years to increase the company's bottom line. MedShare was able to accomplish its mission of solving the global health crisis through helping the most vulnerable.
Companies must redesign their entire supply network to be more customer-centric in order meet consumer needs. Customers can be personalised experiences and products created by using customer-centricity. These networks are vital for both a company's bottom line as well as the global economy. Accenture's supply-chain strategy allows organizations to accelerate their journey towards customer-centricity through targeted commercial interventions and cash flow.
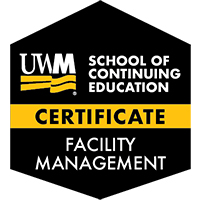
Accenture acquires Alfa Consulting
Accenture recently purchased a consulting firm that specializes in capital-intensive industry operations strategy. Alfa is based out of Spain with offices in Portugal and Spain. Alfa's main focus is on supply chains management and analytical models. This includes tech, energy and capital goods. Accenture's global expansion will bring Alfa to clients' supply chain operations, allowing them to be more efficient and sustainable.
Alfa Consulting will be part of Accenture's Supply Chain & Operations area, where it helps clients achieve customer-centric supply chain segmentation and sourcing transformations. Accenture will provide its own value-based planning and maintenance services in addition to Alfa's supply channel consulting services. Accenture's Iberia supply chains will be strengthened with this acquisition. Accenture still has a strong presence throughout the U.S.
Accenture's acquisition by Xoomworks Group
Accenture announced the acquisition by Xoomworks, a technology- and innovation consulting firm. Accenture's Closed Loop Spend Administration capability is strengthened with this acquisition, which gives clients unprecedented visibility and insight in all price classes. It enhances the ecosystem partners' expertise in digital innovation management. Accenture's acquisition adds a new talent stream to its global talent pools. It has more than 62,000 workers around the world, making it one the largest consulting companies in the world.
The Xoomworks Group was established in 2000 and currently operates two businesses: Xoomworks Procurement, and Xoomworks Technology. The company's Procurement division provides digital procurement and sourcing solutions to clients from all industries. Xoomworks Procurement has more than 250 employees across the UK, France, Germany, and Romania. Accenture states that the acquisition will improve its Closed Loop Spend Management capabilities. Clients can achieve significant, long-term cost savings.
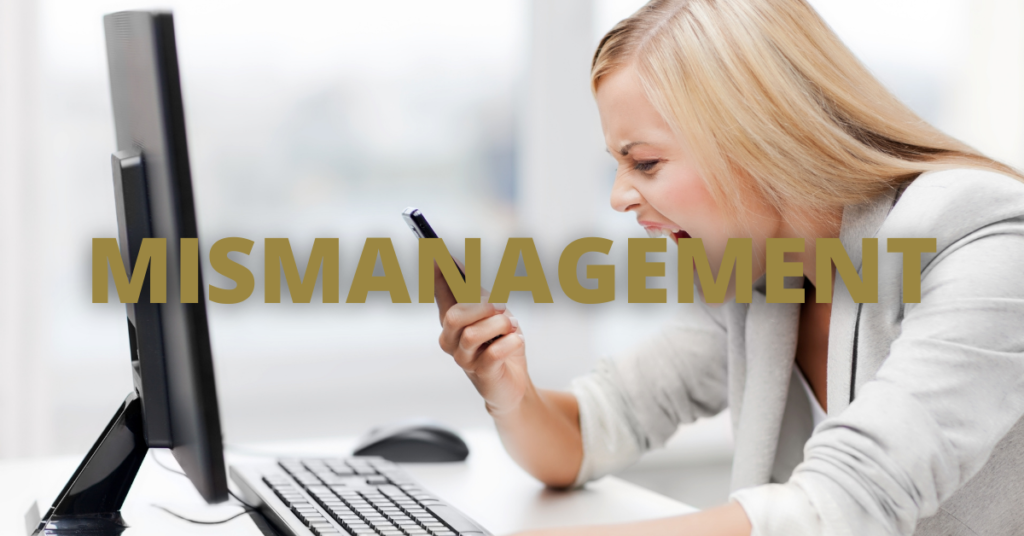
Accenture buys Blue Horseshoe
Accenture has announced that Blue Horseshoe, an integration and supply chain strategy company, will be acquired by Accenture. Blue Horseshoe was founded in 2001 and helps clients in many industries to define their enterprise strategies, connect their applications, and optimize their supply chains. With offices in North Carolina, Ohio, and Estonia, the combined company will offer a range of supply chain solutions. Read on to learn more about the new acquisition.
Accenture has made a number of acquisitions in recent years. This acquisition is just the latest. The consulting giant has become increasingly active in the M&A space, acquiring dozens of companies each year. Accenture had previously acquired data analytics companies and ad agencies. However, it recently purchased LEXTA, a strategic IT consulting firm. This is the company's third largest deal in its history.
FAQ
What role does a manager play in a company?
There are many roles that a manager can play in different industries.
The manager oversees the day-to-day activities of a company.
He/she is responsible for ensuring that the company meets all its financial obligations and produces the goods or services customers want.
He/she makes sure that employees adhere to the rules and regulations as well as quality standards.
He/she is responsible for the development of new products and services, as well as overseeing marketing campaigns.
What is the difference between Six Sigma Six Sigma and TQM?
The major difference between the two tools for quality management is that six Sigma focuses on eliminating defect while total quality control (TQM), on improving processes and decreasing costs.
Six Sigma is a methodology for continuous improvement. It emphasizes the elimination or minimization of defects through statistical methods such control charts and p charts.
This method has the goal to reduce variation of product output. This is done by identifying root causes and rectifying them.
Total quality management involves measuring and monitoring all aspects of the organization. It also includes the training of employees to improve performance.
It is often used to increase productivity.
What is Kaizen?
Kaizen is a Japanese term which means "continuous improvement." This philosophy encourages employees to continually look for ways to improve the work environment.
Kaizen is based on the belief that every person should be able to do his or her job well.
What is a fundamental management tool for decision-making?
A decision matrix is a simple but powerful tool for helping managers make decisions. It allows them to think through all possible options.
A decision matrix is a way of representing alternatives as rows and columns. This allows you to easily see how each choice affects others.
This example shows four options, each represented by the boxes on either side of the matrix. Each box represents one option. The top row displays the current situation, and the bottom row shows what might happen if nothing is done.
The middle column shows the effect of choosing Option 1. It would increase sales by $2 million to 3 million in this instance.
The results of choosing Option 2 and 3 can be seen in the columns below. These are positive changes - they increase sales by $1 million and $500 thousand respectively. But, they also have some negative consequences. For instance, Option 2 increases cost by $100 thousand while Option 3 reduces profits by $200 thousand.
Finally, the last column shows the results of choosing Option 4. This involves decreasing sales by $1 million.
The best thing about using a decision matrix is that you don't need to remember which numbers go where. You just look at the cells and know immediately whether any given a choice is better than another.
The matrix already does all the work. It's as easy as comparing numbers in the appropriate cells.
Here's a sample of how you might use decision matrixes in your business.
Advertising is a decision that you make. This will allow you to increase your revenue by $5000 per month. However, additional expenses of $10 000 per month will be incurred.
You can calculate the net result of investing in advertising by looking at the cell directly below the one that says "Advertising." That number is $15 thousand. Advertising is more valuable than its costs.
Statistics
- Our program is 100% engineered for your success. (online.uc.edu)
- 100% of the courses are offered online, and no campus visits are required — a big time-saver for you. (online.uc.edu)
- Your choice in Step 5 may very likely be the same or similar to the alternative you placed at the top of your list at the end of Step 4. (umassd.edu)
- UpCounsel accepts only the top 5 percent of lawyers on its site. (upcounsel.com)
- The BLS says that financial services jobs like banking are expected to grow 4% by 2030, about as fast as the national average. (wgu.edu)
External Links
How To
How do you do the Kaizen method?
Kaizen means continuous improvement. Kaizen is a Japanese concept that encourages constant improvement by small incremental changes. It's where people work together in order to improve their processes constantly.
Kaizen is one of the most effective methods used in Lean Manufacturing. Kaizen is a concept where employees in charge of the production line are required to spot problems during the manufacturing process before they become major issues. This will increase the quality and decrease the cost of the products.
Kaizen is a way to raise awareness about what's happening around you. Correct any errors immediately to avoid future problems. It is important that employees report any problems they see while on the job to their managers.
There are some basic principles that we follow when doing kaizen. Always start with the end product in mind and work our way back to the beginning. We can improve the factory by first fixing the machines that make it. We then fix the machines producing components, and the machines producing raw materials. Then, we fix those who work directly with the machines.
This method, called 'kaizen', focuses on improving each and every step of the process. After we're done with the factory, it's time to go back and fix the problem.
Before you can implement kaizen into your business, it is necessary to learn how to measure its effectiveness. There are several ways that you can tell if your kaizen system is working. One method is to inspect the finished products for defects. Another way is to see how much productivity has increased since implementing kaizen.
A good way to determine whether kaizen has been implemented is to ask why. Did you do it because it was legal or to save money? You really believed it would make you successful?
Let's say you answered yes or all of these questions. Congratulations! Now you're ready for kaizen.